TECHNOLOGY
&
INNOVATION
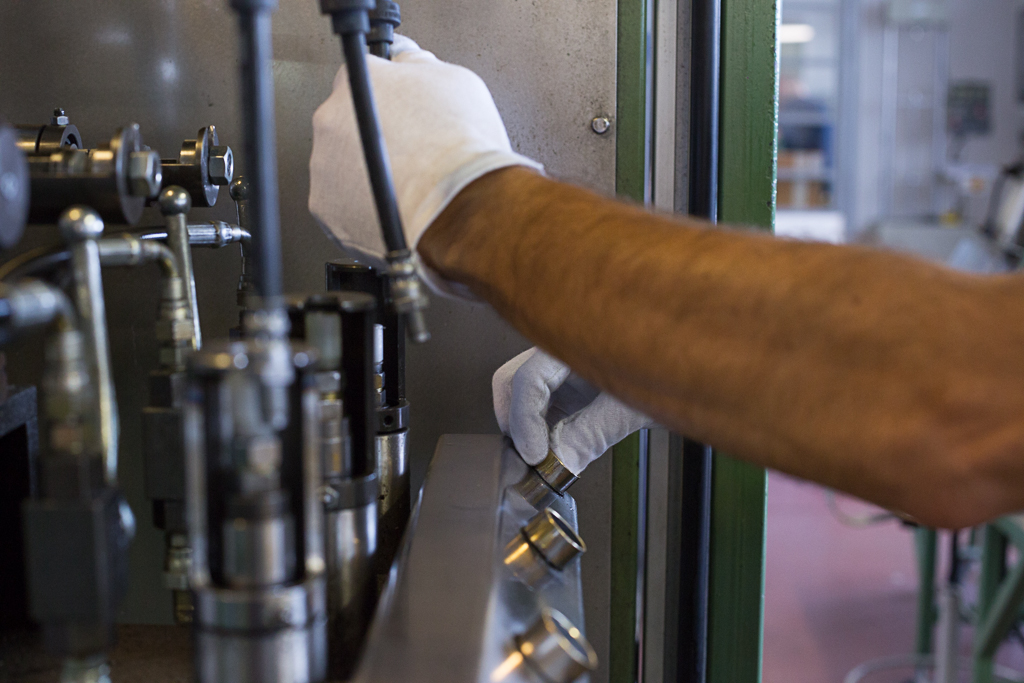
A team dedicated to innovation
Vehicle technology is constantly changing but Flexitech’s priority remains that of safety, so we look to keep one step ahead through continuous improvements to our products and processes. In France and the USA, a team dedicated to innovation works closely with the engineering and sales teams.
DEVELOPMENT PROCESS
1. Research & Innovation, Engineering and Prototyping
- Joint development of specific components and materials with strategic suppliers.
- 70 % of Flexitech’s products are designed and co-designed with OEM partners
- Virtual design process using simulation software
- Rapid prototyping: 3D printing, plasma torch, 3D measuring systems
2. Hose manufacturing processes
- Standardised hose manufacturing processes in all factories
- Manufacturing plants located in 7 different countries
- Hoses developed internally to meet customer requirements
- Automation levels adapted to the country
- Continuous improvement
3. Assembly
- Assembly of hose components (connectors, molding of components, etc.)
- 3 different types of assembly in the group’s plants: automated, semi-automated and manual
- Assembly processes incorporating systematic air pressure tests; 100 % of our products are tested.
4. Tests and laboratory
- A complete battery of tests to meet customer requirements: hot plate, dynamic fatigue rear axle, ASR / ABS, traction test, hot pulse pressure test, cold chamber, tensiometer, volumetric expansion, burst test, saline mist, humidity chamber, durability, whip test, etc.
- Central laboratory for validating new materials, processes and products.
- Front-end simulator for dynamic testing
Industrial technology
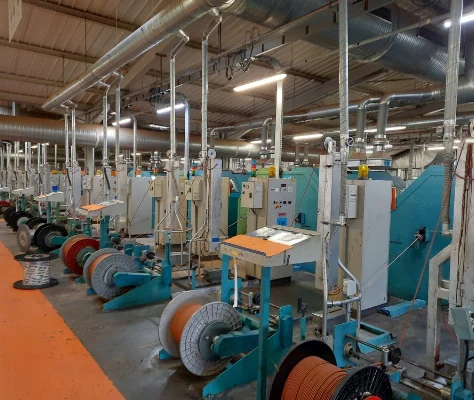
Extrusion: production of hydraulic hoses and pipes
Our expertise includes the extrusion of inner hoses, compound inner tubes, including braiding, vulcanisation, cutting and packaging. Our manufacturing processes are automated to guarantee consistent quality.
Assembly
Assembly of components and overmolding of hoses and pipes
A complex combination of industrial expertise allows us to use 3 assembly methods (automated, semi-automated and manual) for all the components used in our hoses: crimping, cold forming, overmolding, bending, etc.
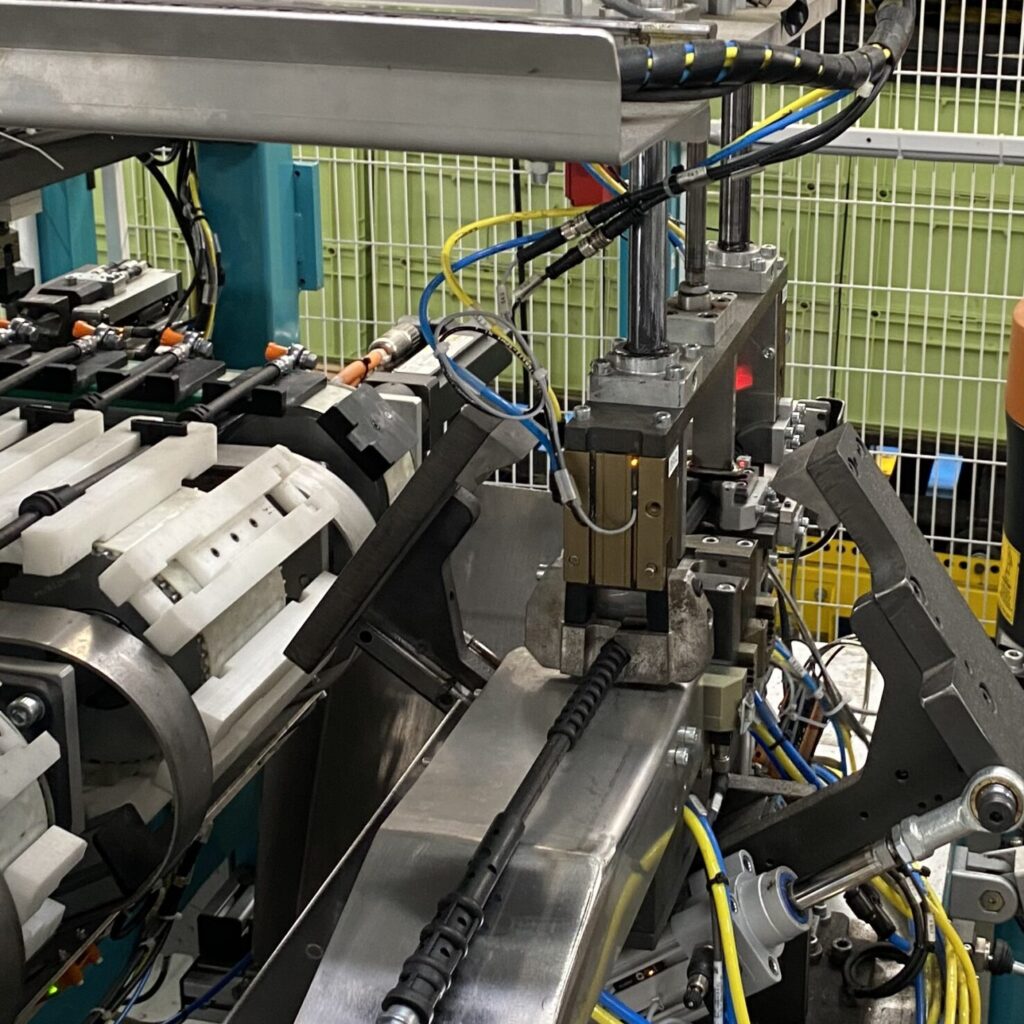